We Take Quality Seriously
You want knowledgeable people when you call for precast concrete products. You can be confident that we have the most experienced team in the industry. Our employees, company-wide, have been serving customers for over 35 years at Advance Concrete Products. The majority of our experienced crew has been working here 20+ years!
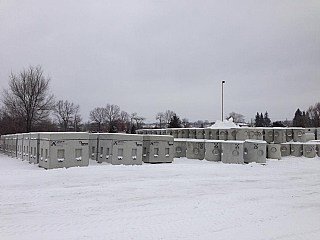
Advance Concrete Products begins preparing for winter production in the summer. During even the coldest months, we pour the highest quality precast products. Our expert production crew casts concrete handholes, manholes, interceptors, tunnels, etc. in our environmentally controlled facility, increasing inventory for the busy, warmer months, and keeping the contractors happy that layer up and work no matter the season. Our experienced drivers deliver in winter so you can get your project wrapped up quickly in the cold weather. We will arrive on-time to unload with our trailer mounted cranes on your snowy jobsite, so when the warmer temperatures finally arrive for a couple days, you can get other work done. It's not always sunny outside, and we know you must get some projects finished in bad weather. Let Advance Concrete Products make it easier for you.
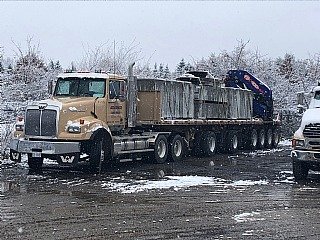
Certifications
ACI Certified for Field Testing
NPCA Production and Quality School
Advance Concrete Products Co. has multiple people on staff that have completed the National Precast Concrete Association's Production and Quality School, taking the refresher at intervals recommended by the NPCA to keep the information fresh.
Associations
Membership in a variety of professional organizations allows Advance Concrete Products to learn about coming trends and the latest innovations.
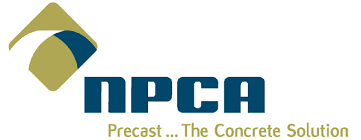
National Pre-cast Concrete Association
NPCA
Our involvement in the NPCA enables us to offer our clients the latest innovations in product and service. At the same time, it gives them peace of mind knowing they are dealing with a plant that is rigorously inspected by an outside firm with extremely high standards.
For 31 consecutive years, Advance Concrete Products has been awarded status as a National Precast Concrete Association (NPCA) Certified Plant. Advance is also one of the longest continuously certified plants in North America, having passed all inspections since 1991. We are proud to announce a 99% score resulting from our April 2022 unannounced NPCA plant inspection. We congratulate our entire team on achieving an A+!
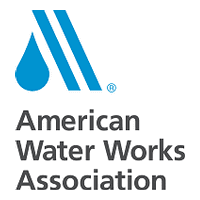
The American Water Works Association
AWWA
ACP has been a member of the Michigan Section of the AWWA since 2002, an organization whose primary focus is to ensure safe, adequate and reliable drinking water. Membership in the AWWA, allows us to learn about coming trends. It also allows us to maintain a close connection with our customers and understand the challenges and issues they face.
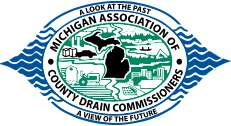
Michigan Association of County Drain Commissioners
MACDC
The Michigan Association of County Drain Commissioners is dedicated to protection of the health, safety, and welfare of Michigan's citizens, their lands and environmental quality, and to the protection and restoration of Michigan's water resources. They seek to accomplish these goals by promoting professional development and education, encouraging member involvement, and continually improving Drain Commissioners' implementation of their myriad responsibilities by promoting the latest standards, technologies and methods for storm water management, water resource protection, drainage, financial management, customer service, and public administration
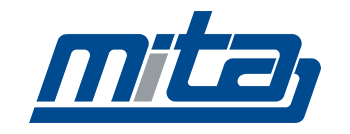
Michigan Infrastructure and Transportation Association
MITA
MITA is a statewide construction trade association formed in 2005 through the merger of Associated Underground Contractors and the Michigan Road Builders Association. The membership consists of nearly 800 Michigan companies representing construction disciplines such as road and bridge, sewer and water, utility, railroad, excavation and specialty construction.
Specifications
PART 1 - GENERAL
1.1 SECTION INCLUDES
A. This specification covers the materials for and manufacture of precast reinforced concrete units produced in accordance with the plans and these specifications.
1.2 REFERENCES - Where applicable, the latest editions of the following standards shall be considered a part of these specifications. In case of conflict, these specifications shall take precedence over the listed standard. (See also Article 2.4, Concrete Materials)
A. American Association of State Highway and Transportation Officials (AASHTO)
1. “Standard Specification for Highway Bridges”
2. “Guide Specifications for Structural Design of Sound Barriers”
B. ACI 304 – Guide for Measuring, Mixing, Transporting and Placing Concrete
C. ACI 318 - Building Code Requirements for Reinforced Concrete
D. ASTM C478 - Specification for Precast Reinforced Concrete Manholes Sections
E. ASTM C825 - Standard Specification for Precast Concrete Barriers
F. ASTM C857 - Standard Practice for Minimum Structural Design Loading for Underground Precast Concrete Utility Structures
G. ASTM C858 - Standard Specification for Underground Precast Concrete Utility Structures”
H. ASTM C890 - Standard Practice for Minimum Structural Design Loading for Monolithic or Sectional Precast Concrete Water and Wastewater Structures
I. ASTM C913 - Standard Specification for Precast Concrete Water and Wastewater Structures
J. ASTM C915 - Standard Specification for Precast Reinforced Concrete Crib Wall Members
K. ASTM C923 – Standard Specification for Resilient Connectors Between Reinforced Concrete Manhole Structures, Pipes and Laterals
L. ASTM C936 - Standard Specification for Solid Concrete Interlocking Paving Units
M. ASTM C990 - Standard Specification for Joints for Concrete Pipe, Manholes and Precast Box Sections Using Preformed Flexible Joint Sealants
N. ASTM C1227 - Standard Specification for Precast Concrete Septic Tanks
O. ASTM 1433 - Standard Specification for Precast Reinforced Concrete Box Sections for Culverts, Storm Drains, and Sewers
P. ASTM C1478 - Standard Specification for Storm Drain Resilient Connectors Between Reinforced Concrete Storm Sewer Structures, Pipes and Laterals
Q. AWS D1.1 - Structural Welding Code - Structural Steel
R. AWS D1.4 - Structural Welding Code - Reinforcing Steel
S. CRSI Manual of Standard Practice
1.3 FRANCHISE PRODUCTS
A. Products manufactured under franchise arrangements shall conform to all the requirements specified by the franchiser. Items not included in the franchise specification but included in this specification shall conform to the requirements in this specification.
1.4 SUBMITTALS
A. Product Data
1. For standard precast concrete units, the precast concrete producer will supply cut sheets showing conformance to project drawings and requirements and to applicable ASTM specifications listed in this specification. The Precast concrete producer shall certify that such products will meet the ASTM specifications.
2. For proprietary precast concrete units, the precast concrete producer may supply standard plans or informative literature. Supporting calculations and design details shall be available upon request. The Precast concrete producer shall warrant that such products will perform the intended task.
B. Shop Drawings
1. The plans for custom-made precast concrete units shall be shop drawings furnished by the precast concrete producer for approval by the Owner or his agent (specifier). These drawings shall show complete design, installation, and construction information in such detail as to enable the Owner to determine the adequacy of the proposed units for the intended purpose. Details of steel reinforcement size and placement as well as supporting design calculations, if appropriate, shall be included. The drawings shall include a schedule, which will list the size and type of precast concrete units at each location where they are to be used. The precast concrete units shall be produced in accordance with the approved drawings.
1.5. QUALITY ASSURANCE
A. Precast concrete producer shall demonstrate adherence to the standards set forth in the National Precast Concrete Association Quality Control Manual. Precast concrete producer shall meet requirements written in subparagraph 1 or 2.
1. NPCA Certification - The precast concrete producer shall be certified by the National Precast Concrete Association's Plant Certification Program prior to and during production of the products for this project.
2. Qualifications, Testing and Inspection
a. The Precast concrete producer shall have been in the business of producing precast concrete products similar to those specified for a minimum of 5 years. The precast concrete producer shall maintain a permanent quality control department or retain an independent testing agency on a continuing basis. The agency shall issue a report, certified by a licensed engineer, detailing the ability of the precast concrete producer to produce quality products consistent with industry standards.
b. The Precast concrete producer shall show that the following tests are performed in accordance with the ASTM standards indicated. Tests shall be performed for each 150 cu. yd. of concrete placed, but not less frequently than once per week.
1. Slump: C143
2. Compressive Strength: C31, C192, C39
3. Air Content (when air-entrained concrete is being used): C231 or C173
4. Unit Weight: C138
c. The Precast concrete producer shall provide documentation demonstrating compliance with this subparagraph.
d. The Owner may place an inspector in the plant when the products covered by this specification are being manufactured.
1.6 DELIVERY, STORAGE AND HANDLING
A. Handling
1. Products shall be stored, handled shipped and unloaded in a manner to minimize damage. Lifting holes or inserts shall be consistent with industry standards. Lifting shall be accomplished with methods or devices intended for this purpose.
B. Acceptance at Site
1. The Owner's representative shall make final inspection and acceptance of the precast concrete products upon arrival at the jobsite.
PART 2 - PRODUCTS
2.1 MANUFACTURERS
A. The precast concrete manufacturer must meet the guidelines written in article 1.5 paragraph A.
2.2 MANUFACTURED PRECAST UNITS
A. Precast Concrete: Provide all units shown in Contract Documents and as needed for a complete and proper installation
B. Design Criteria - Design units in accordance with:
1. _______________ building code.
2. ACI 304 and 318.
3. CRSI Manual of Standard Practice.
4. Applicable ASTM Standard(s).
C. Finishes
1. Formed non-architectural surfaces: Surfaces cast against approved forms using industry practice in cleaning forms, designing concrete mixes, placing and curing concrete. Normal color variations, form joint marks, small surface holes caused by air bubbles, and minor chips and spalls will be tolerated but no major imperfections, honeycombs or other defects will be permitted.
2. Unformed surfaces: Surfaces finished with a vibrating screed, or by hand with a float. Normal color variations, minor indentations, minor chips and spalls will be tolerated but no major imperfections, honeycombs, or other defects shall be permitted.
3. Special finishes:
a. Troweled, broom or other finishes shall be according to the requirements of project documents and performed per industry standards or supplier specifications.
b. Precast concrete producers shall submit finishes for approval when required by the project documents. The sample finishes shall be approved prior to the start of production.
D. Patching and Repairs
1. No repair is required to formed surfaces that are relatively free of air voids and honeycombed areas, unless the surfaces are required by the design to be finished.
2. Repairing Minor Defects - Defects that will not impair the functional use or expected life of a manufactured precast concrete product may be repaired by any method that does not impair the product.
3. Repairing Honeycombed Areas - When honeycombed areas are to be repaired, all loose material shall be removed and the areas cut back into essentially horizontal or vertical planes to a depth at which coarse aggregate particles break under chipping rather than being dislodged. Proprietary repair materials shall be used in accordance with the manufacturer's instructions. If a proprietary repair material is not used, the area shall be saturated with water and, immediately prior to repair, the area should be damp, but free of excess water. A cement-sand grout or an approved bonding agent shall be applied to the chipped surfaces, followed immediately by consolidating an appropriate repair material into the cavity.
4. Repairing Major Defects - Defects in precast concrete products which impair the functional use or the expected life of products shall be evaluated by qualified personnel to determine if repairs are feasible and, if so, to establish the repair procedure.
2.3 MATERIALS
A. Concrete - Concrete shall be a uniform mix of quality materials listed in Article 2.4. Mix proportions shall be determined by following the standards in ACI 318 Chapter 5. Recommendations for selecting proportions for concrete are given in detail in Standard Practice for Selecting Proportions for Normal, Heavyweight, and Mass Concrete (ACI 211.1). Recommendations for lightweight concrete are given in Standard Practice for Selecting proportions for Structural Lightweight Concrete (ACI 211.2).
1. Water-Cement Ratio
a. Concrete that will be exposed to freezing and thawing shall contain entrained air and shall have water-cement ratios of 0.45 or less. Concrete which will not be exposed to freezing, but which is required to be watertight, shall have a water-cement ratio of 0.48 or less if the concrete is exposed to fresh water, or 0.45 or less if exposed to brackish water or sea water. For corrosion protection, reinforced concrete exposed to deicer salts, brackish water or seawater shall have a water-cement ratio of 0.40 or less.
2. Air Content
a. The air content of concrete that will be exposed to freezing conditions shall be within the limits given in Table 1.
Table 1 Total Air Content For Frost-Resistant Concrete
Nominal Maximum
Aggregate Size (Inches) Air Content, %
Severe Exposure Moderate Exposure
3/8 6.0 to 9.0 4.5 to 7.5
1/2 5.5 to 8.5 4.0 to 7.0
3/4 4.5 to 7.5 3.5 to 6.5
1 4.5 to 7.5 3.0 to 6.0
1-1/2 4.5 to 7.0 3.0 to 6.0
*For specified compressive strengths greater than 5000 psi, air content may be reduced 1%.
3. Compressive Strength
a. All concrete shall develop a minimum compressive strength of 4,000 psi in 28 days unless other strengths are designated on the drawings.
B. Portland Cement: ASTM C150, Type I, II, III or V.
C. Aggregates: ASTM C33 or C330.
D. Water: Potable or free of deleterious substances in amounts harmful to concrete or embedded metals.
E. Admixtures:
1. Air-entraining: ASTM C260
2. Water reducing, retarding, accelerating, high range water reducing: ASTM C494
3. Pozzolans, fly ash and other mineral admixtures: ASTM C618
4. Ground granulated blast furnace slag: ASTM C989
5. Pigments: Non-fading and lime-resistant
2.4 REINFORCEMENT AND CONNECTION MATERIALS
A. Provide all reinforcement, accessory and connection materials required. Concrete reinforcement shall be steel bars or welded wire fabric, or a combination thereof.
B. Reinforcing Bars:
1. Deformed Billet-steel: ASTM A615
2. Deformed Rail-steel: ASTM A616
3. Deformed Axle-steel: ASTM A617
4. Deformed Low-alloy steel: ASTM A706
C. Reinforcing Wire:
1. Plain Wire: ASTM A82
2. Deformed Wire: ASTM A496
D. Welded Wire Fabric:
1. Plain Wire: ASTM A185
2. Deformed Wire: ASTM A497
E. Epoxy Coated Reinforcement:
1. Reinforcing Bars: ASTM A775
2. Wires and Fabric: ASTM A884
F. Galvanized Reinforcement:
1. Reinforcing Bars: ASTM A767
G. Inserts and Embedded Metal - All items embedded in concrete shall be of the type required for the intended task, and meet the following standards:
1. Structural steel plates, angles, etc: ASTM A36
2. Proprietary items: In accordance with manufacturers published literature
3. Welded studs: AWS D1.1
4. Finishes (as required):
a. Shop primer: Manufacturers' standards
b. Hot-dipped galvanized: ASTM A152
c. Zinc-rich coating: MIL-P-2135 self-curing, one component, sacrificial
d. Cadmium coating: Manufacturers' recommendations
H. Joint Sealant and Joint Gaskets:
1. Joints for Circular Concrete Sewer and Culvert Pipe, Using Rubber Gaskets: ASTM C443.
2. External Sealing Bands for Noncircular Sewer, Storm Drain, and Culvert Pipe: ASTM C877.
3. Joints for Concrete Pipe, Manholes, and Manufactured Box Sections Using Preformed Flexible Joint Sealants: ASTM C990
4. Specification for Elastomeric Joint Sealants: ASTM C920
I. Pipe Entry Connectors:
1. Resilient Connectors Between Reinforced Concrete Manhole Structures, Pipes and Laterals: ASTM C923.
J. Grout:
1. Cement grout: Portland cement with enough water for the required strength and sand for proper consistency. May contain mineral or chemical admixtures, if approved by Owner's representative.
2. Non-shrink grout: Premixed, packaged expansive and non-expansive shrink- resistant grout.
2.5 FABRICATION
A. Forms for manufacturing precast concrete products shall be of the type and design consistent with industry standards. They should be capable of consistently providing uniform products and dimensions. Forms shall be constructed so that the forces and vibrations to which the forms will be subjected can cause no product damage.
1. Forms shall be cleaned of concrete build-up after each use.
2. Form release agents shall not be allowed to build up on the form casting surfaces.
B. Reinforcement
1. Cages of reinforcement shall be fabricated either by tying the bars, wires or welded wire fabric into rigid assemblies or by welding where permissible in accordance with AWS D1.4. Reinforcing shall be positioned as specified by the design and so that the concrete cover conforms to requirements. The tolerance on concrete cover shall be one-third of that specified but not more than 1/2 in. Concrete cover shall not be less than 1/2 in. Positive means shall be taken to assure that the reinforcement does not move significantly during the casting operations.
C. Embedded Items
1. Embedded items shall be positioned at locations specified in the design documents. Inserts, plates, weldments, lifting devices and other items to be imbedded in precast concrete products shall be held rigidly in place so that they do not move significantly during casting operations.
D. Placing Concrete
1. Concrete shall be deposited into forms as near to its final location as practical. The free fall of the concrete shall be kept to a minimum. Concrete shall be consolidated in such a manner that segregation of the concrete is minimized and honeycombed areas are kept to a minimum. Vibrators used to consolidate concrete shall have frequencies and amplitudes sufficient to produce well consolidated concrete.
2. Cold Weather Requirements - Recommendations for cold weather concreting are given in detail in Cold Weather Concreting reported by ACI Committee 306.
a. Adequate equipment shall be provided for heating concrete materials and protecting concrete during freezing or near-freezing weather.
b. All concrete materials and all reinforcement, forms, fillers, and ground with which concrete is to come in contact shall be free from frost.
c. Frozen materials or materials containing ice shall not be used.
d. In cold weather the temperature of concrete at the time of placing shall not be below 45° F. Concrete that freezes before its compressive strength reaches 500 psi shall be discarded.
3. Hot Weather Requirements - Recommendations for hot weather concreting are given in detail in Hot Weather Concreting reported by ACI Committee 305.
a. During hot weather, proper attention shall be given to ingredients, production methods, handling, placing, protection, and curing to prevent excessive concrete temperatures or water evaporation that could impair required strength or serviceability of the member or structure. The temperature of concrete at the time of placing shall not exceed 90° F.
E. Curing
1. Curing by Moisture Retention - Moisture shall be prevented from evaporating from exposed surfaces until adequate strength for stripping (Article 2.6, paragraph F) is reached by one of the following methods:
a. Cover with polyethylene sheets a minimum of 6 mils thick.
b. Cover with burlap or other absorptive material and keep continually moist.
c. Use of a membrane-curing compound applied at a rate not to exceed 200 sq. ft. per gallon, or per manufacturers' recommendations.
2. Surfaces that will be exposed to weather during service shall be cured as above a minimum of 3 days. Forms shall be considered effective in preventing evaporation from the contact surfaces. If air temperature is below 50°F the curing period shall be extended.
3.Curing with Heat and Moisture
a. Concrete shall not be subjected to steam or hot air until after the concrete has attained its initial set. Steam, if used, shall be applied within a suitable enclosure, which permits free circulation of the steam. If hot air is used for curing, precautions shall be taken to prevent moisture loss from the concrete. The temperature of the concrete shall not be permitted to exceed 160° F. These requirements do not apply to products cured with steam under pressure in an autoclave.
F. Stripping Products from Forms
1. Products shall not be removed from the forms until the concrete reaches the compressive strength for stripping required by the design. If no such requirement exists, products may be removed from the forms after the final set of concrete provided that stripping damage is minimal.
G. Shipping Products
1. Products shall not be shipped until they are at least 5 days old, unless it can be shown that the concrete strength has reached at least 75% of the specified 28-day strength, or that damage will not be caused which will impair the performance of the product.
2.6 SOURCE QUALITY CONTROL
A. Fabricate units in accordance with ACI 318 and the National Precast Concrete Association's Quality Control Manual for Precast Plants.
PART 3 - EXECUTION
3.1 INSTALLATION
A. Site Access
1. General contractor shall be responsible for providing adequate access to the site to facilitate hauling, storage and proper handling of the precast concrete products.
B. Installation
1. Precast concrete products shall be installed to the lines and grades shown in the contract documents or otherwise specified.
2. Products shall be lifted by suitable lifting devices at points provided by the precast concrete producer.
3. Products shall be installed per the precast concrete producer's recommendation.
C. Water tightness
1. Where water tightness is a necessary performance characteristic of the precast concrete product's end use, watertight joints, connectors and inserts should be used to ensure the integrity of the entire system.
3.2 FIELD QUALITY CONTROL
A. Site tests - when testing is required for an underground product, one of the following methods need to be followed:
1. Vacuum testing prior to backfill according to ASTM C1244.
2. Water testing according to contract documents and precast concrete producer's recommendations.
This specification is intended solely for use by professional personnel who are competent to evaluate the significance and limitations of the information provided herein, and who will accept total responsibility for the application of this information. The National Precast Concrete Association disclaims any and all responsibility and liability for the accuracy of and the application of the information contained in this publication to the full extent permitted by law.